Hot pressing sintering is a unique type of special sintering technology, with its history dating back to the 1920s. At that time, German scientists first applied it to the preparation of hard alloys, marking the beginning of its application in the field of materials science. In principle, hot pressing sintering is essentially a dry pressing process under high-temperature conditions. Although its specific forms are diverse, the core process is largely the same: filling the powder material into a mold, applying pressure to the powder through upper and lower punches while heating, and achieving simultaneous forming and sintering.
Compared with pressureless sintering, hot pressing sintering has many significant advantages. Since heating and pressurizing are carried out simultaneously, it can not only reduce the forming pressure but also lower the sintering temperature, shorten the sintering time, and inhibit grain growth. The resulting products typically have fine grains, high density, and excellent mechanical and electrical properties. More importantly, without the need for sintering or forming additives, hot pressing sintering can produce ultra-high-purity ceramic products. For some ceramic materials that are difficult to densify under pressureless sintering conditions, such as carbides, borides, and nitrides, hot pressing sintering can also achieve densification.
So, what is the mechanism of hot pressing sintering? From a theoretical perspective, the hot pressing sintering process can generally be divided into two stages: the rapid densification stage and the slow densification stage.
The rapid densification stage mainly occurs in the early period of hot pressing sintering. In this stage, the main densification mechanisms are grain rearrangement and plastic deformation. From a microscopic structural perspective, the contact area between particles is very small at this time. The stress formed by the external pressure in the microstructure is highly concentrated, resulting in a large effective pressure. This pressure will lead to two results: one is that grains slide and rearrange to achieve more effective close packing; the other is that when the stress at the grain contact area exceeds the material's yield strength, plastic yielding will occur, increasing the contact area. Under high-temperature conditions, materials will soften, and plastic yielding will occur even if the pressure is not particularly high, especially for metallic or amorphous glass materials. When the pressure is sufficiently high, plastic deformation can occur even at low temperatures or room temperature, significantly increasing the density of the sample. For example, when copper powder is subjected to a pressure of 3 GPa at room temperature, the resulting sample density can reach 99%. However, the density achieved at the end of the rapid densification stage depends on the nature of the sintering material and is not a fixed value. If the material is soft or a liquid phase is formed during the sintering process, a higher density can usually be achieved, and even complete densification is possible. However, if the material does not easily undergo plastic deformation, the density achieved in this stage will be relatively low. When sintering nano-ceramics, if the external pressure is low and the temperature is not high, grain rearrangement may not even occur. However, regardless of the final density achieved, a common feature of this stage of sintering is that the grain size does not change significantly and does not grow noticeably.
After the rapid densification stage, the slow densification stage begins. The main densification mechanism in this stage is creep. Creep refers to the deformation that occurs in materials under stress below the yield strength over time. From a microscopic perspective, creep occurs because atoms migrate from the compressed regions of the grains to the tensile regions, and this migration is mainly accomplished through diffusion. Depending on the diffusion mechanism, creep can be divided into volume diffusion creep and grain boundary diffusion creep. Under high-temperature and high-pressure conditions, volume diffusion creep is more important; however, if the temperature is not particularly high, grain boundary diffusion creep often dominates. At this time, grain size has a significant impact on the creep rate. Studies have shown that during hot pressing sintering at 50 MPa and 1200°C for 1 hour, the density of Al₂O₃ ceramic with a grain size of 0.5 micrometers can reach about 82%, while that with a grain size of 2.0 micrometers can only reach about 28%. In addition to diffusion, creep can also be caused by dislocation movement, although this phenomenon is more common in the sintering of metallic materials.
In fact, the sintering mechanisms mentioned above are not unique to hot pressing sintering. They are also present in all sintering processes with pressurization, such as hot forging and hot isostatic pressing (HIP). However, there are some differences in the details. For example, in hot forging, since the sample is not restricted by the mold, grain sliding and plastic deformation are more pronounced. In hot isostatic pressing, although the pressure appears to be very uniform, this uniformity is only at the macroscopic level. At the microscopic level, it is not uniform, so plastic deformation or creep can still occur. Moreover, since the pressure in hot isostatic pressing is usually much higher than that in hot pressing, densification is more easily achieved.
Hot pressing sintering, with its unique advantages and mechanisms, plays an important role in the field of material preparation. With continuous in-depth research and technological progress, it is believed that hot pressing sintering will shine in the production of more high-performance materials and provide strong support for the development of modern industry.
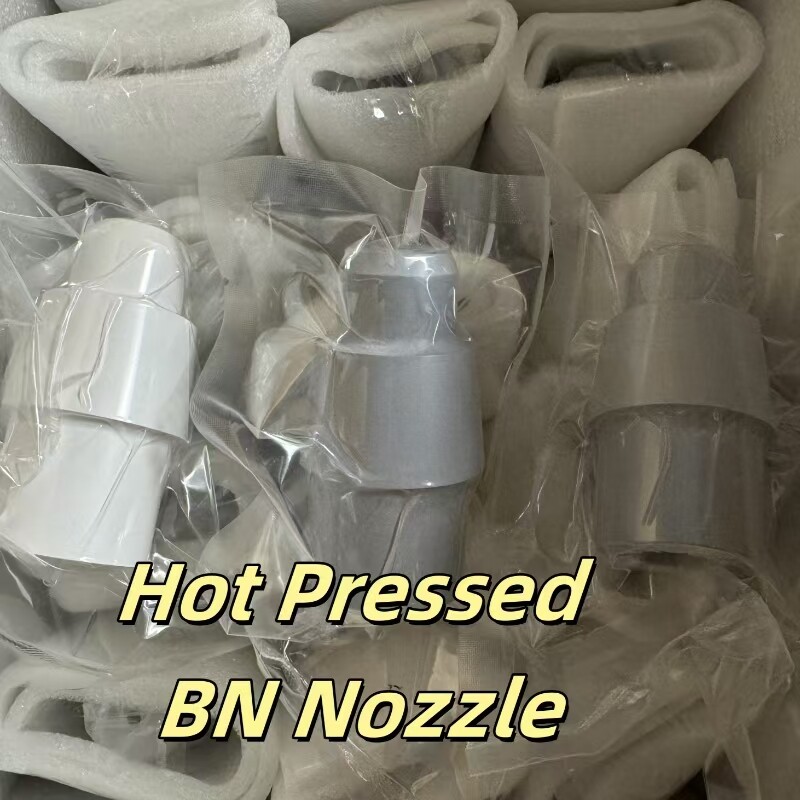