Alumina ceramics are a high-performance ceramic material with α-Al₂O₃ as the main crystal phase. With its high melting point, high hardness, heat resistance, corrosion resistance and excellent electrical insulation, it has shown excellent application value in many fields. This material is not only inexpensive, but also has a mature production process, so it has become one of the ceramic materials with the largest output and the widest application. From cutting tools, wear-resistant parts to bioceramics, to energy, aerospace, chemical engineering and electronics, alumina ceramics are everywhere. In particular, alumina 95 ceramics and 99 ceramics are one of the ceramic materials with the widest application range and the largest consumption, whether in the field of structural ceramics or electronic ceramics.
However, the preparation process of alumina ceramics is relatively complicated, involving multiple production processes. The material is easily contaminated during frequent contact with machinery, equipment, tools, utensils and the environment, which leads to quality problems of ceramic parts. Among them, color problems are particularly common, mainly including the following situations:
1. Spots
(I) Common phenomena
During the production process of alumina porcelain, black, brown, brown and pink spots often appear on the surface of the porcelain, and are also found inside from time to time. These spots are one of the important reasons for the failure of alumina porcelain products.
(II) Cause analysis
Through electron microscopy, energy spectrum analysis or chemical analysis, it can be found that the main impurity components of black, brown and brown spots are iron (Fe), while the main impurities of pink spots are iron (Fe), chromium (Cr) and nickel (Ni). Further tracking of the production process and production process shows that black, brown and brown spots are mostly caused by mechanical iron particles mixed in the raw materials and ceramic production process; pink spots are mostly caused by fine particles of stainless steel materials. There are two main ways for mechanical impurities to mix in: one is that there are problems with the raw materials themselves; the other is that they are contaminated during the production process.
(III) Prevention and solution measures
During the compression molding stage, the following points should be noted:
Raw material selection: Raw materials with good quality and low iron content should be used first, and magnetic separation and iron removal should be carried out when necessary.
Grinding stage: Check the lining bricks of the ball mill regularly to see if they have fallen off. If they have, they should be repaired in time to avoid impurities from being mixed in due to damage to the lining bricks.
Granulation process: Install a magnetic separation and iron removal device during the slurry transportation process, and optimize the hot air furnace and hot air filtration system to prevent rust in the hot air system from entering the material. Before the final product is packaged, the granulated powder is magnetically separated to remove iron to ensure product purity.
Pipeline protection: All conveying pipelines should be lined with polyurethane as much as possible to reduce the risk of impurities from mixing in due to pipeline wear.
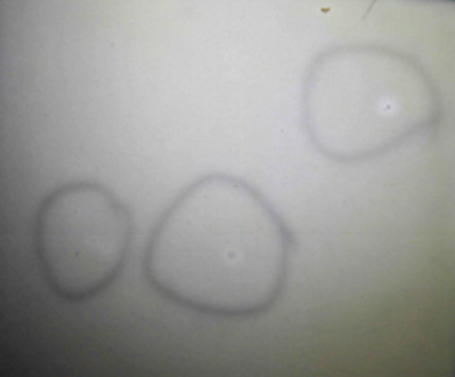
2. Dark spots (negative spots, cloud spots, oil spots, etc.)
(I) Common phenomena
During the production process of 95 porcelain, a dark spot defect sometimes occurs, which is also called negative spots, cloud spots, oil spots, etc. This dark spot varies in shape and size, and some can even occupy more than half of the area of the porcelain. They usually appear on tubular porcelain or relatively thick and large porcelain, especially on porcelain produced by granulation and isostatic pressing. Dark spots are usually hidden inside the porcelain and can only be found under light. In severe cases, they will also appear on the surface of the porcelain.
(II) Cause Analysis
The reasons for the dark spots in 95 porcelain are relatively complicated, but it is clear that this phenomenon is not caused by impurities in the raw materials, but is closely related to the formula, production process and production technology of the ceramics.
(III) Prevention and solution measures
For the dark spot problem, it is necessary to analyze it according to the specific situation of the production site and take the following basic measures:
Optimize the firing curve: formulate a reasonable firing curve to ensure that the porcelain has sufficient debinding temperature and time during the firing process to avoid the generation of dark spots due to insufficient debinding.
Strengthen kiln exhaust: maintain a proper oxidizing atmosphere in the kiln, and ensure the stability of the gas environment during the firing process by strengthening the design and optimization of the exhaust system to reduce the dark spot problem caused by abnormal atmosphere.
Adjust the firing temperature: within the firing temperature range, try to increase the firing temperature as much as possible, or appropriately extend the residence time in the high temperature section. This helps to improve the density and uniformity of the porcelain, thereby reducing the appearance of dark spots.
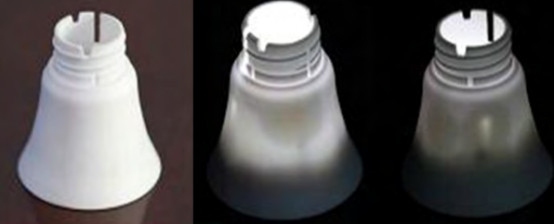
3. Bright spots
(I) Common phenomena
Alumina porcelain (95 porcelain, 99 porcelain) thin-sheet porcelain pieces, especially those produced by tape casting, sometimes have bright spots. The size of these bright spots is generally between 1 and 2 mm, and they are particularly obvious under light.
(II) Causes
With the help of a microscope with a magnification of more than 100 times, it can be found that the surface of the porcelain piece at the bright spot is concave. Because the concave part is thinner and has a higher light transmittance, bright spots are produced. Judging from the shape and structure of the concave part, bright spots are mostly caused by mechanical damage, such as mechanical damage caused by adhesion between the substrate blank and the base tape or other reasons during the tape casting process.
(III) Prevention and solution measures
During the production, storage and movement of the blank, special attention should be paid to avoid mechanical damage. By optimizing the production process and strengthening the skills training of operators, the standardization and refinement of the production process can be ensured, thereby reducing the probability of bright spots.
IV. Color difference
(I) Common phenomena
Alumina 95 porcelain is usually white, but the whiteness will be slightly different due to different formulas. However, during the production process, it is sometimes found that some porcelain parts are gray. This phenomenon usually occurs in the whole batch and is not easy to detect when observed individually. It can only be found when compared with normal porcelain parts. Although there is no obvious difference in the electrical and mechanical properties of porcelain parts, the color difference between batches may cause users to question and thus affect the sales of products.
(II) Cause discussion
The color difference of alumina porcelain parts is mainly caused by impurity pollution introduced during the production process. From the selection of raw materials to each link in the production process, any tiny impurity mixed in may affect the color of porcelain parts.
(III) Prevention and solution measures
Optimize the grinding process: adjust the grinding process parameters, select grinding media with lower abrasiveness, and find the best material-to-ball ratio, grinding time and mill operating parameters through experiments. This can not only reduce the wear of porcelain balls and porcelain linings, but also effectively reduce the introduction of impurities during the grinding process, thereby improving the color consistency of porcelain parts.
Improvement of hot die casting: During the hot die casting process, the wax removal powder should be replaced regularly, and special wax removal powder should be selected to avoid contamination of the ceramic blank during the wax removal process, ensuring the purity and color uniformity of the ceramic.
4. Yellowing of color
(I) Common phenomena
Under normal circumstances, alumina ceramics should be white after firing, but in many cases they will show a light yellow color. According to industry insiders, this yellowing phenomenon will become more obvious with the increase of alumina content and the improvement of the density of ceramics. In addition, after exposure to sunlight, the color of the ceramics will further deepen, and the degree of yellowing will be more significant compared with unexposed ceramics.
(II) Cause analysis
Although many people have conducted tests on this phenomenon, the exact cause has not yet been found. However, it is generally believed that there may be the following factors:
The influence of sunlight exposure: After exposure to sunlight, the composition inside the alumina ceramic may undergo irreversible changes, resulting in color changes.
Deliquesce phenomenon: Alumina ceramics may undergo deliquesce, thereby generating hydrated alumina. This phenomenon not only occurs in ceramic products, but also in other materials. Therefore, the problem of discoloration of alumina precision ceramics can only be alleviated by minimizing the influence of external factors.
Influence of sintering aids: Ceramics with high alumina content (more than 99%) mainly use solid-phase sintering process. Sintering aids are dissolved into oxide crystals and enriched on the grain boundaries, resulting in a decrease in crystal purity and a yellow-based color. In addition, due to surface lattice defects and other reasons, the surface is in a metastable state and is prone to adsorbing various fine substances, thus causing discoloration.
产品页面
点击这里联系我们!